
Gaining Efficiency in Picking – A Case Study
A long-time client of ours invited us to consult and assist on a warehouse project focused on Picking Optimization. The client is a global textile giant that primarily produces and manages home goods, like linen, apparel, and accessories.
This client’s definition of Picking Optimization summed up as:
- Gain Speed – look for every opportunity to speed up the process
- Support Accuracy – build a process flow that encourages accuracy
- Maintain Dependability – always remember to meet or exceed customer’s expectations
The client brought in our team specifically to study the current picking process and design a plan for improvement. We immediately found that the actual picking process was only partially to blame for the operation’s ‘picking’ inefficiencies. In other words, it wasn’t the actual act of picking that was creating the bulk of the inefficiencies.
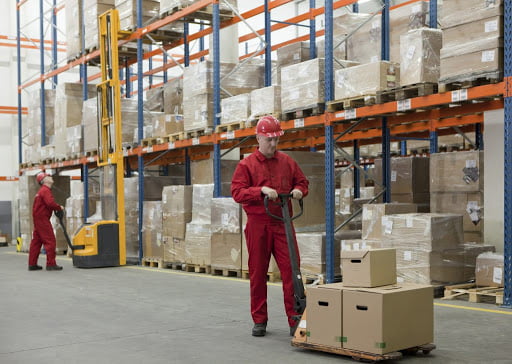
In this context we will define ‘Picking’ here as:
The action of physically pulling the inventory for the customer’s order from the warehouse location to prepare it for shipping.
The Initial Discovery
To get the most from the client’s picking process, we first had to evaluate the existing processes and gather data to analyze it. The client was already capturing data on things like:
- Units Picked per Hour, by user
- Backorders daily detail

They were capturing the data, but no one had been taking time to analyze that data as it applied to the operation. There were no time studies, no productivity standards, no-cost analysis, and therefore no real way to grade the process. A big part of our efforts would be to analyze the available data, design new reporting tools, and determine the appropriate productivity expectations.
One of the most valuable things we do, as a project team, is to talk to the people closest to the process. The Picking Team was eager to share their pain points, which was a great place to start. Talk to people about what frustrates them, and you will generally find out opportunities to improve your processes. Our team spent several weeks shadowing the employees in each area, Picking, Replenishment, and Inventory Control. They documented current flow, exceptions, and built relationships with key players. We were getting familiar with what was working well and what wasn’t. In each functional area, the goal was to listen to the employees, document their struggles, their successes, and see where we could make changes that could have a significant positive impact overall.
Here were the major complaints coming directly from Pickers:
- Inefficient Processes/Too many steps
- Equipment Issues (Scan Guns, Forklifts)
- Slow and or ‘missing’ Replenishments
- Pick Location Sequencing Issues
- Inventory Issues
The Project Highlights

After taking in all the information provided by the client in addition to the onsite analysis and associate shadowing,
we proposed and implemented the following solutions:
Paper vs. RF – Make the Switch to RF Picking to reduce the handling time for Pickers. This not only reduces paper waste, but it is a much smoother communication tool to keep workers focused on the next task at hand. Our client’s Warehouse Management System (WMS) was capable of being configured to use Tasking (work assignments), which allows leadership to have a more relevant real-time form of control.
Pick to Carton vs. Batch Picking – We found that in certain areas of the warehouse, we were able to gain efficiencies in batch picking instead of picking straight into outbound cartons. For the smaller eCommerce orders, it made more sense to pick into totes moving in a single path through the warehouse, eliminating the need to revisit a popular location over and over again in the same shift.
Full Case/Pallet Picking – By making some configuration changes, we took advantage of larger order quantities and, when possible pull that order from the ‘case’ or ‘pallet’ inventory instead of ‘unit’ inventory. Pulling a boxed case is much more efficient than picking units. If the case qty is 5 and the order is for 21, it’s a lot more practical for pickers to pull 4 cases and 1 loose unit than to pull 21 loose units.
RF Equipment
The existing RF Equipment was aging and unreliable. Period. A simple solution to eliminate the issue was to upgrade all the existing RF and auxiliary equipment to the most current available technology. This included:
- Wrist RF units for picking – upgrading from the old handheld units to wearables. This allowed the users to go hands-free, which not only gave them added speed but the ability to focus and develop a smoother workplace rhythm without constantly stopping and laying the unit down, causing loss of units, incomplete transactions, and distractions, etc.
- Forklift mounted units – for similar reasons to above, the addition of the mounted RF devices on the forklifts allows users to focus on the task at hand, and not juggle cumbersome equipment which costs time, efficiency and safety issues.
- Wireless Network – The wireless network and RF Access Points were upgraded for greater speed and reliability. Additional access points were placed in the warehouse to support the growing RF usage.
Pick Sequencing
Next, we looked at the sequencing of the locations during picking. This particular warehouse originally had the Pick locations sequenced by the actual location number. In some areas of the warehouse this was working well. In other areas, we saw a need to alter the sequencing to allow picking ‘odd’ or ‘even’ sides of the aisle separately. The change was made without altering the location name, but by updating a miscellaneous field in the file to control the picking sequence.
Active Pick Location Slotting
One of our strategies also involved ‘Slotting Efficiently’. The idea is that the items with the highest sell-through-rate, or velocity, are maintained in the prime positions for ease and speed of picking. Often prime item SKUs are put in the larger location, easily accessible and easy to move product in and out quickly. SKUs that have a more extended history can use that information to anticipate future moves required. The slotting strategy has a direct impact on picking affecting order demand, which in turn controls the pickers’ efficiency in their movements.
Material Handling Equipment
Powered MHE (Forklifts, PowerJacks) – Every piece of equipment had to be thoroughly inspected and repaired/replaced. Daily inspections and key control systems were implemented.
Non-Powered MHE (Carts, Handjacks, etc.) – Every piece of equipment was fully inspected and repaired/replaced.
Perform Location, Slotting and Storage Analysis
Active Pick Location Review
One of the first things we looked at was the Active Pick Location specifications within the system. We adjusted Location minimums and maximums, location volume, and dimensions, etc. Validating the critical aspects of the active picking location ensures that inventory is putaway to fulfill the most capacity possible. In this instance, our client found several hundred sites with incorrect specifications that had been impacting picking by having such a low maximum. This caused the replenishments to come in one case at a time instead of the needed pallet quantities. This further added to the struggle of completing the Replenishments on time to keep the picker going.
Pick Sequencing
Next, we looked at the sequencing of the locations during picking. This particular warehouse originally had the Pick locations sequenced by the actual location number. In some areas of the warehouse this was working well. In other areas, we saw a need to alter the sequencing to allow picking ‘odd’ or ‘even’ sides of the aisle separately. The change was made without altering the location name, but by updating a miscellaneous field in the file to control the picking sequence.
Active Pick Location Slotting
One of our strategies also involved ‘Slotting Efficiently’. The idea is that the items with the highest sell-through-rate, or velocity, are maintained in the prime positions for ease and speed of picking. Often prime item SKUs are put in the larger location, easily accessible and easy to move product in and out quickly. SKUs that have a more extended history can use that information to anticipate future moves required. The slotting strategy has a direct impact on picking affecting order demand, which in turn controls the pickers’ efficiency in their movements.
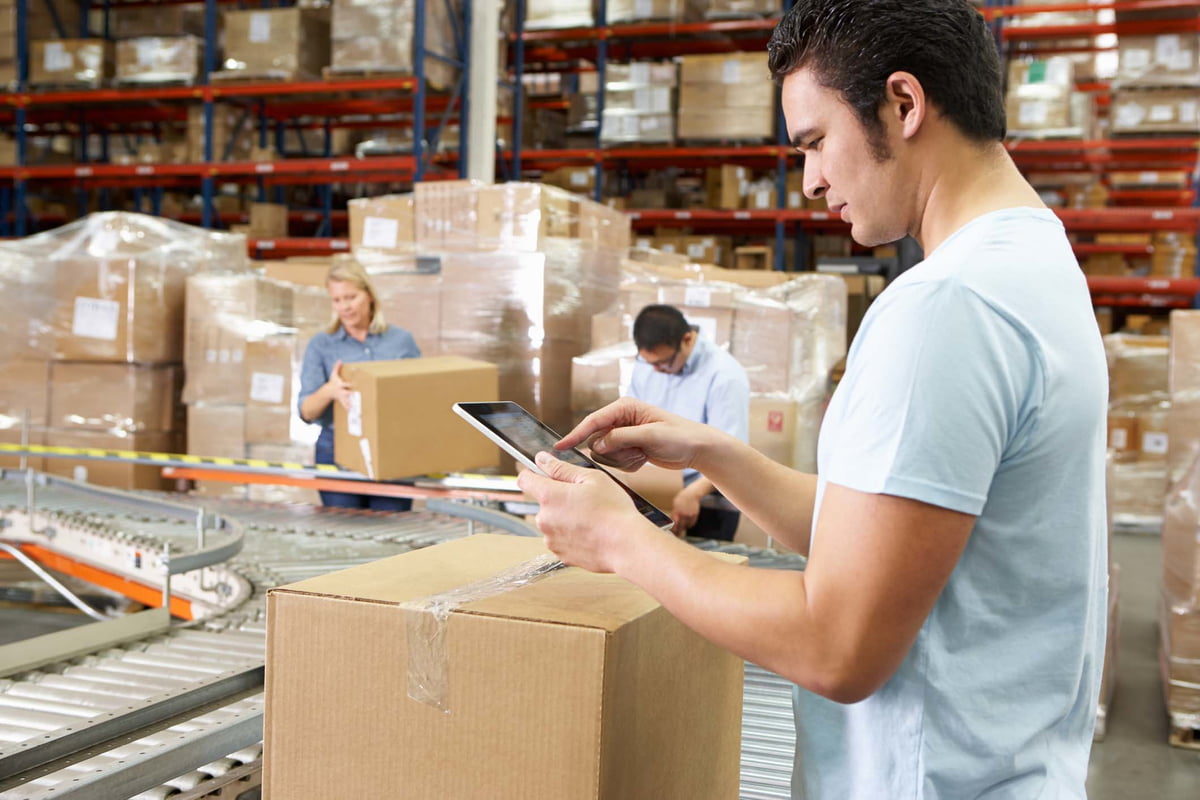
Slotting Systems versus Report Data
Our client was using report data to show the velocity for the SKUs they had slotted to the active pick locations. The report was being run but not acted upon regularly. So, one of the solutions we implemented here was; reading and reacting. A team was assigned to check the report daily to look for opportunities to adjust the active slotting, meaning they might more dynamically relocate inventory in and out of the prime pick zones.
Reserve Inventory Storage
The team also decided to adjust the reserve inventory layout to support the speedy replenishment of the pick locations. They developed a plan to store a portion of the reserve inventory in adjacent areas of the warehouse as the Active Picking Location. This will speed the replenishment process reducing the travel time for the warehouse team. In some parts of the warehouse, since the picking location was only the bottom rack location, we were able to permanently assign the same SKU into the reserve locations directly above the Active Pick location. This allowed users to make a very quick move to replenish the active picking inventory.
Review and Enhance the Replenishment Strategy
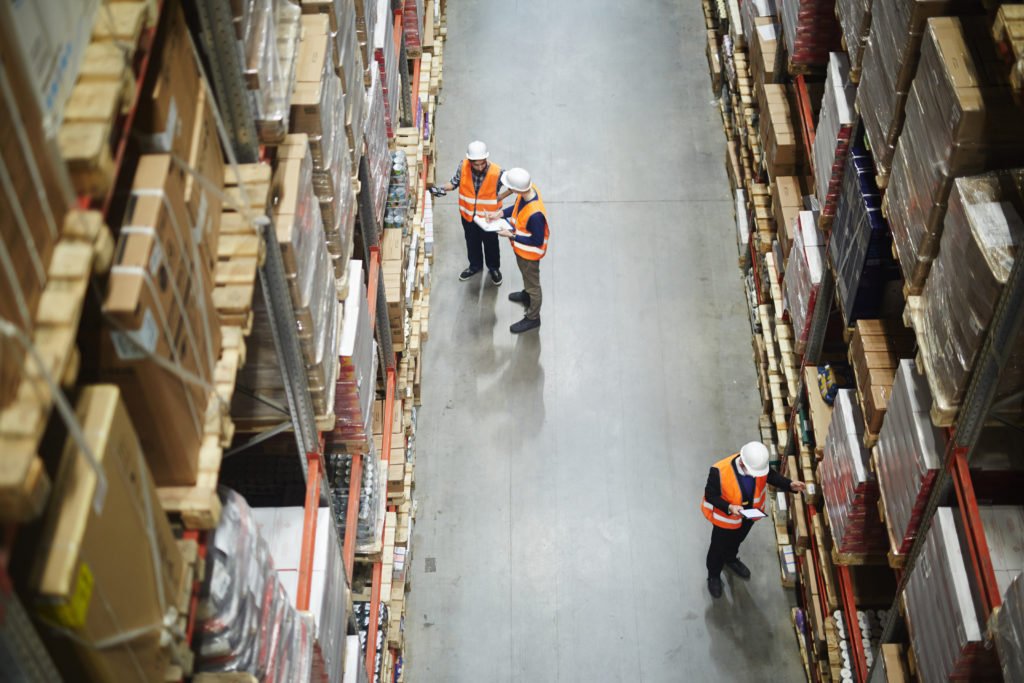
Probably the best way to keep the pickers moving is to make sure there is always plenty of inventory to pick. A process we call replenishment ensures the pick locations are filled methodically. When orders are processed to the warehouse floor, or waved, the system performs an analysis of the current pickable inventory. Further, it determines based on the order demand, how much more inventory will be needed for the picking to be entirely fulfilled from the active Pick Location. The last step in this process is the system creates tasks for users to bring the required inventory to the location.
To improve the timeliness of wave replenishment, we made some configuration changes to allow certain areas in the warehouse to fill to the Location Maximum with the wave. Previously, the client was replenishing only the demand quantity for that particular wave. This was a reasonable process for the bigger waves. With an onslaught of small waves they were getting too many small replenishment tasks within same day when a couple larger tasks to keep the location full would have been more efficient.
We also implemented a Lean-time Replenishment process. This allowed a user to trigger replenishments anytime without an order demand. A screen in the system will enable them to set some criteria like location range or starting location, number of locations, etc. The user then submits a job that attempts to create replenishment tasks that fill the selected locations to their full capacity. This is often a convenient option for keeping locations topped-off because it can be done in the slower hours of the shift.
Improve Inventory and Quality Control
Cycle Counting
Regular inventory maintenance dramatically reduces the occasion of inventory shortages. Our client had established processes and rules for inventory management but needed help putting them into action and the follow-through. With the renewed focus on picking integrity, the inventory team was motivated to improve its accuracy as well.
We also added some supplementary system-generated Task counts, which are driven by events in locations such as short picks. This allows the inventory team to immediately resolve any picking issue before additional users encounter the same location issue.
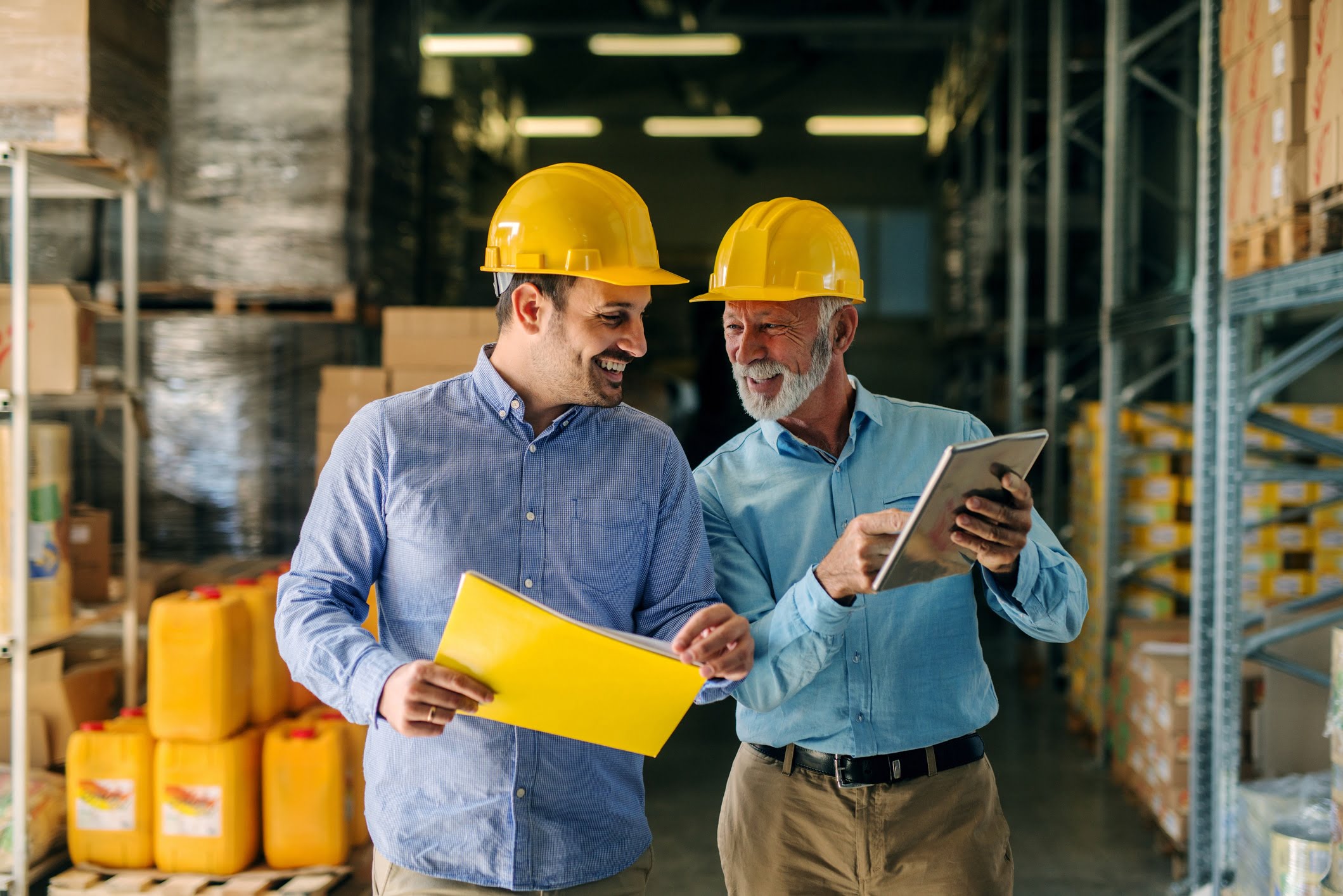
Outbound Carton Audits
In addition to giving us the chance to improve a customer’s experience, the addition of outbound carton audits provided a multitude of coaching opportunities to correct quality issues from the picking and packing process. We used the system to flag 10% of every picker’s work for a quality check. It keeps the pickers focused on accuracy as well as speed.
The Results and conclusion
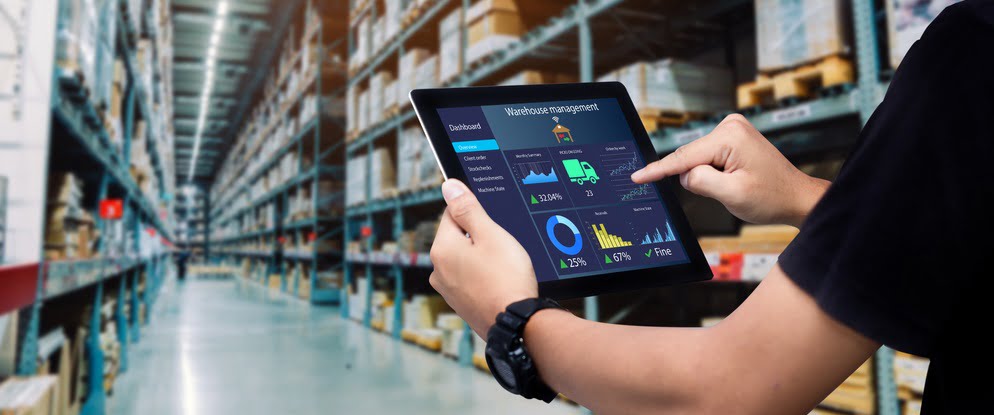
Overall the Picking optimization project was a huge success for our client. The project covered all the basic issues reported by the workers, as well as meeting the client’s requirements of increasing Speed, Accuracy, and Dependability. This project was unlike some in that many of the elements were reasonably simple to deploy, and most gave immediate results. The client reported that within the first 6 months after the project:
Those are pretty impressive numbers! To find out more about how a Katalyst’s supply chain team can help refine your picking operation, click the Get In Touch button below.